It’s revolutionary. For the first time ever we can design a thing, send the digital 3D model file to a printer, and then print it in perfect, accurate 3D. The results are awesome and the potential is inspiring. Whatever sector you design in you’ll probably want to know how to design for 3d printing. This guide reveals all about what is actually a pretty simple process. By the end of it you’ll understand how to design 3d models for printing, get some top tips for 3D printing design, and enjoy a quick tour around the wonderful world of SketchUp, one of the world’s best-loved 3D design tools.
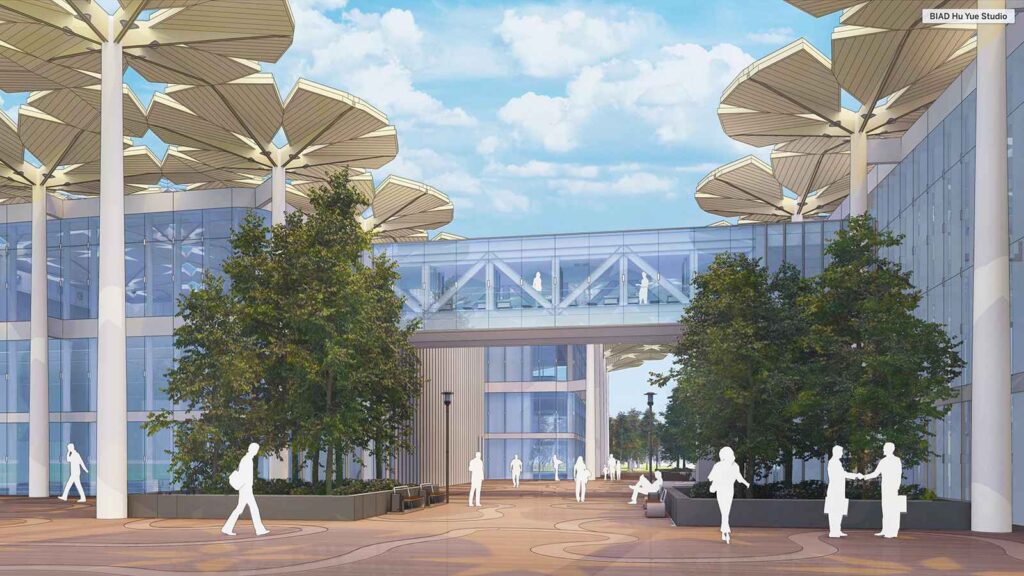
How to Design 3D Models for Printing
3D printing is sometimes called additive manufacturing. It simply means making solid 3 dimensional objects from a digital file using an additive process. The printer lays down layers of molten material, adding more until the object is complete. Every layer is a thin cross-section of the thing you’re printing.
This way of working costs less than traditional manufacturing, bringing the cost of 3d parts, models and prototyping right down as well as putting it in the hands of anyone with a suitable 3D printer. 3d printing improves success rates, reduces waste, and speeds up product development.
3D print is exciting because you can print complex 3D shapes directly and see them develop as you watch, a fascinating process in itself. Take note of these essential best practice tips and you’ll be a step ahead from the offset. Here’s how to design for 3d printing.
Figure out the build volume – which affects the size of the things you can print. Basically if your design is bigger than the printer can print, it won’t print. You need to know this before you begin designing to save yourself time and hassle. If your design needs more printer capacity it isn’t the end of the world. You can break it up into manageable parts called modules and print them separately.
Choose the right orientation – Fused Filament Fabrication or FFF describes the way the print material extrudes, where the object is built up of melted material layer after layer. Because FFF prints layer by layer you need to decide the orientation early on because it influences your design choices.
No sharp corners – You can probably see it in your mind’s eye. Sharp corners come with powerful shrinking forces which kick in as the print cools. It can easily warp, whereas rounded corners don’t tend to because they spread the forces to lessen the risk.
Think about overhang supports – FFF printed parts can cope with overhangs, but there’s a practical limit. When you want to stop layers from drooping or curling on your overhangs, don’t print unsupported
overhangs at an angle less than 50° from the vertical axis down. Take care over overhang quality too, which can depend on the material. Some need support at lower angles than others.
Know your bridging supports – Bridging support guidelines are crucial. Always make un-supported horizontal bridges 10mm or less to print problems and failures.
What’s the nozzle size and hole size? – The printer nozzle size matters. Bigger nozzles print faster and the nozzle size also drives the design’s minimum height and wall thickness. Hole size is another important thing. The best way to success is simply avoid modelling holes less than 2 mm diameter so you can be sure they don’t get blocked up.
Top Tips for 3D Printing Design
Now you know how to design 3d models for printing. Next, here are some high-level tips for 3D printing design.
First, choose the right 3D modeling software. SketchUp is a great pick for all sorts of reasons, including the fact it’s used by every imaginable sector where 3D design is a thing.
Second, choose the right materials for your 3D printing project. Will it be a resin-based material or the most common, plastic? State-of-the-art machines usually use fine powdered material for a highly detailed finish. You might choose a metal, or even carbon fibre. You’ll probably enjoy the learning process.
Third, follow all the 3d printing design guidelines and rules to hit the success button, like those we’ve talked about above. There’s no need to experiment and fail when others have done the hard work before you!
And fourth, like you would with any project, double check your design before pressing the print button. Find any problems, fix them, then check the file one last time.
Choosing the Right Software - How to Use SketchUp for 3D Printing
SketchUp is one of the world’s most popular 3D modeling and design programs for 3D printing. So how to use SketchUp for 3D printing? We’ll keep it simple with a step-by-step guide.
- Set your template properly – It’s a potentially expensive and embarrassing mistake to make, so first set your template to metric or imperial, millimetres or inches. Do it like this: Window > Preferences > Template > 3D Printing – Millimetres or 3D Printing – Inches
- Install a free SketchUp STL extension like the SimLab STL Importer for SketchUp or SketchUp STL. The STL file format is the most common in 3D printing, used by most people so ideal for sharing, editing and printing designs with other software. A SketchUp STL extension means you can export your model to a 3D printer as an STL file
- Follow tried and tested 3d printing design guidelines, in other words avoid thin surfaces and walls, make your model watertight and solid, and steer clear of internal overlaps
- Take a look at your model from the inside – this is where you might find hidden mistakes that mean the model can’t be printed. Use SketchUp’s Entity Info feature to know more, using Select and Hide to see inside the model. Or switch into x-ray-mode by clicking on View > Face Style > X-ray
- Make an outer shell – As we’ve said, overlapping objects cause problems in 3d printing.
- But when you create an outer shell it automatically deletes all the internal overlapping parts
- Fix your faces – If the surface of your model is facing in the wrong direction, usually facing the inside of the object instead of the outside, the software changes the colour of the surfaces to pale blue for you. To fix it all you do is right-click on the inside surface then select Reverse Faces
- Make curves smoother by increasing your circle and arc segments, just as simple to fix
- Zoom in close – It’s useful to know that some problems are so tiny it’s hard to see them without zooming in. It’s worth spending time checking the small stuff, but there’s an easier way. SketchUp extensions like Solid Inspector 2 find problems automatically and show you where they are
There’s an exciting feature in the SketchUp 3D Warehouse. When you upload a model to it, tick the ‘I want this to be 3D printable’ button and it fixes any modeling errors instantly, which means you can safely download it as an STL file then let the 3D print magic begin
A true renaissance woman
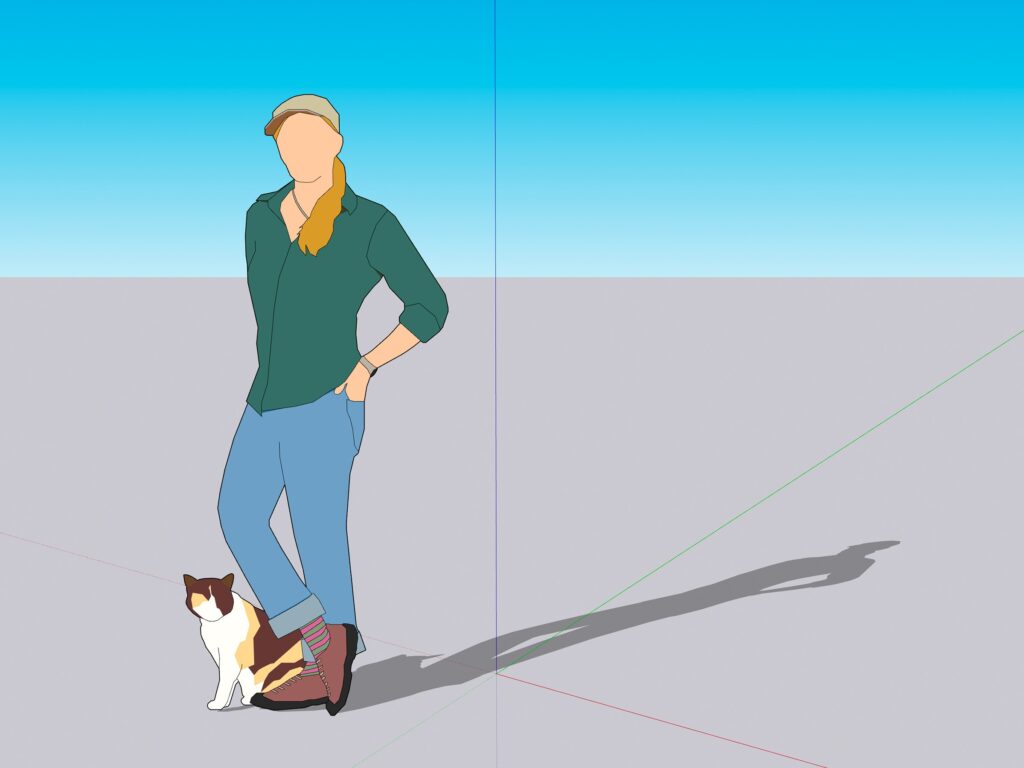
SketchUp Pro Plans and Pricing
Now you know how to design 3d models for printing and how to use SketchUp for 3d printing. If you’re inspired to design and print something amazing in 3D , check out the ins and outs of the free and Pro versions of SketchUp here. You can order a free trial of SketchUp Pro here, or subscribe and buy SketchUp Pro right away on the same page. There are countless excellent extensions here, as well as a good choice of SketchUp licensing options with special licenses for commercial design, higher education, primary schools and secondary schools.